Look Out For Leakers: How To Reduce Your Risk of Leaking Cans
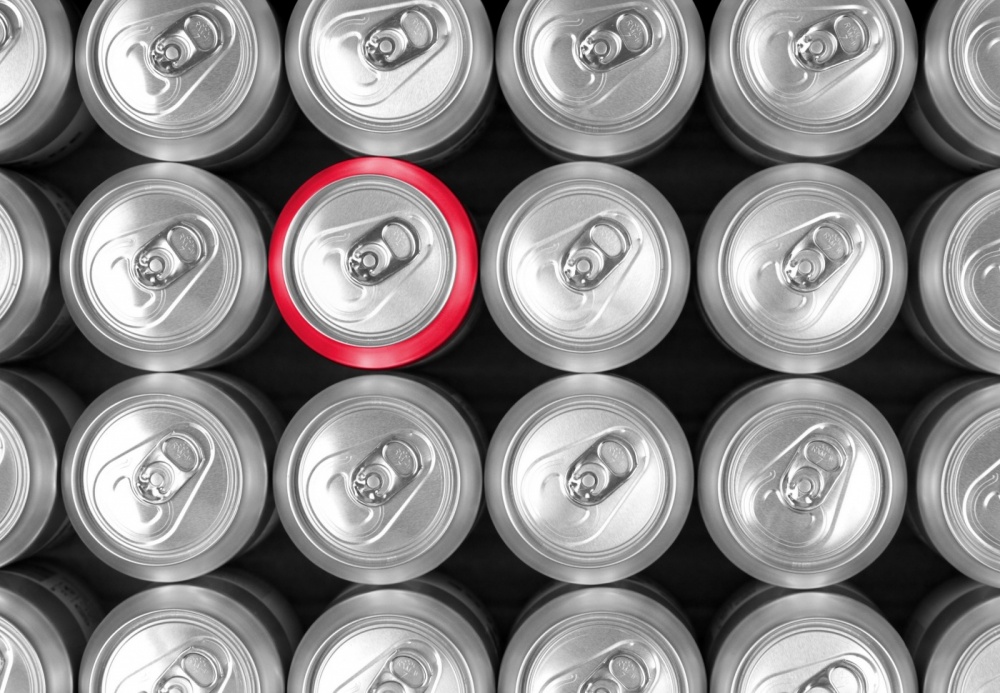
Leaking cans are not a common occurrence. But it only takes one encounter with the aftermath of “leakers,” as they are often referred to in the industry, to understand why you hope you never see one again.
"Beware of little expenses; a small leak will sink a great ship." -Benjamin Franklin
Although rare, just one small leak can cause significant problems for a beverage brand. Leaking cans, or "leakers," as they are commonly called in the industry, have the potential to damage other products and ruin a brand's reputation. While it's easy to think it won't happen to you, you could see a leaking can issue at some point in your beverage career without the proper precautions. The good news is that learning more about leakers and what causes them can help you better understand and manage your beverage brand's overall can quality.
"Leakers happen for a lot of different reasons. A calm, organized approach to investigating potential root causes often reveals several opportunities to tighten up and improve processes, quality, and efficiency," says Smith.
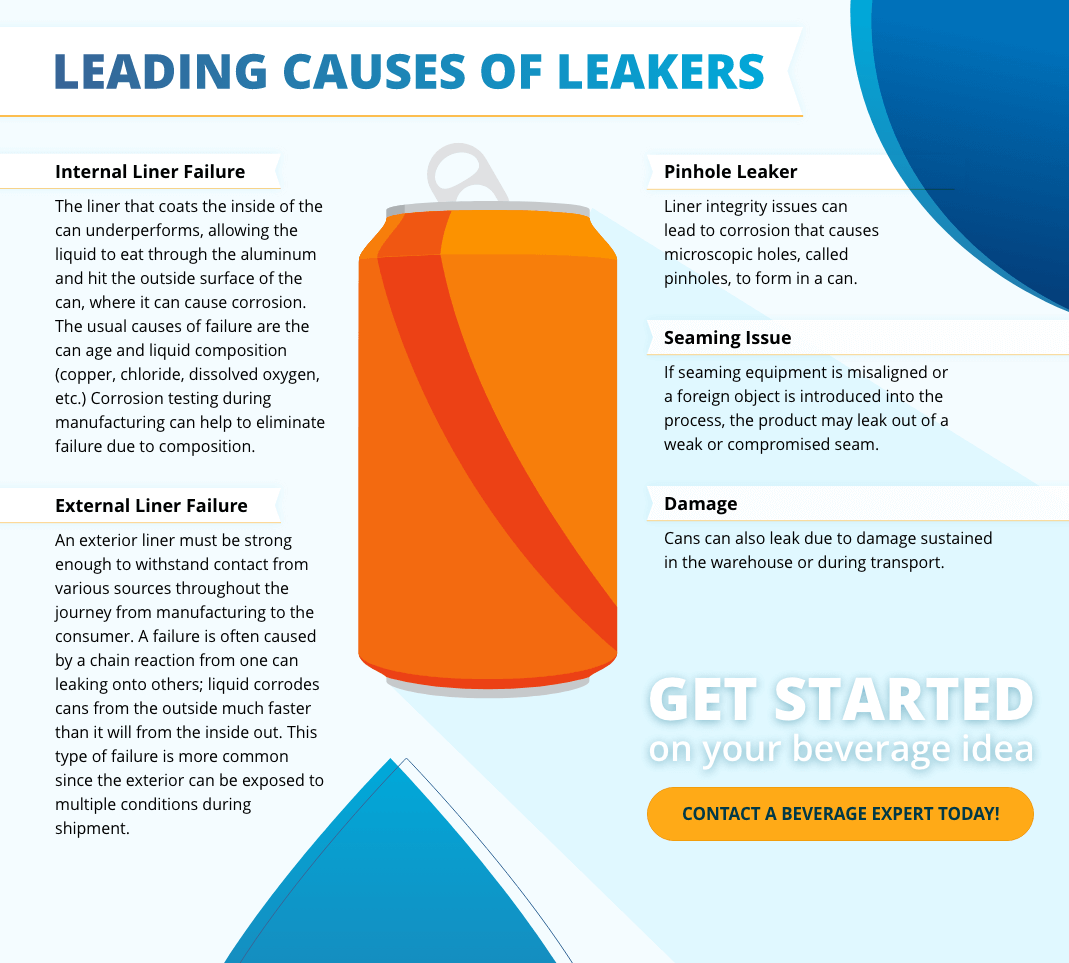
Leading Causes of Leakers
A leak happens anytime a substance that is supposed to be held within the can spills or seeps out. While the consequences are ultimately visible in the form of less-than-perfect products, the root causes of leakers can be complex. Here are some of the primary issues that lead to leakers:
Internal Liner Failure
An internal liner failure is when the liner that coats the inside of the can underperforms, allowing the liquid to eat through the aluminum and hit the outside surface of the can, where it can cause corrosion. This type of breakdown is commonly known as secondary corrosion and is the primary cause of leaking cans. The outer liner doesn’t prevent corrosion, but an external liner failure can expedite a leaking can problem.
External Liner Failure
Cans also have an exterior liner that needs to be strong enough to withstand contact from various sources throughout the journey from manufacturing to the consumer. Leaks from an internal or external liner failure can impact the outer packaging of any other products the liquid touches. Not every can supplier maintains the same quality standards. But, tools like the SpecMetrix® ACS coating thickness and film weight measurement system empower beverage makers to independently diagnose potential issues and ensure product packaging consistency.
Pinhole Leaker
Liner integrity issues can lead to corrosion that causes microscopic holes, called pinholes, to form in a can. With a pinhole leaker, you often see the liquid that's escaped, but it can be challenging to find the tiny hole it traveled through.
Seaming Issue
A seamer creates a continuous seam between the lid and the can, creating a tight seal for the contained product. If seaming equipment is misaligned or a foreign object is introduced into the process, the product may leak out of a weak or compromised seam.
Damage
Cans can also leak due to damage sustained in the warehouse or during transport. While it’s vital to palletize your products properly for maximum protection by using enough wrap and reinforcement, sometimes that isn’t enough. Damage to cans can happen more easily when the liner's integrity is compromised due to changes in pressure and pH caused by certain microorganisms. It’s difficult to overstate the importance of effectively rinsing your cans with properly pasteurized water. Any product left on the outside of the can could quickly start secondary corrosion.
Get in Touch With a Beverage Specialist Now
Eight Reasons Every Beverage Brand Should Be Scared of Leakers
If you bring up the topic of leaking cans in a room of beverage industry veterans, you’re bound to hear some scary stories. We asked a group of BevSource specialists to share what worries them most about the prospect of a leaking can. Their experiences reflect the fact that, although the probability of leaking cans is small, the damage they can do is anything but insignificant. Here are eight solid reasons brands shouldn’t let their guard down when it comes to leakers.
1. It’s Hard to Know When a Leaker is Lurking Around the Corner
It’s true; most brands will never face a leaker. If you follow proper protocols and quality checks, it’s unlikely that a leaking can will ever turn up in your supply chain. But even slight variations in your can supply or subtle changes to your formula, packaging process, transportation, or storage situation can be enough to trigger a leaking issue you might never have anticipated.
Over her five years in the beverage industry, Erin Marvin-Barnes, Manager of Client Services at BevSource, has only had to tackle a few leakers, but she remembers them well. “Nobody wants to get a call like that,” says Marvin-Barnes, who has helped find the root cause of leaking can issues for brands. “As soon as you know you have a leaker, the clock is ticking. You’re just trying to contain the damage as quickly as you can.”
2. The Root Causes of Leakers are Often Illusive
As difficult as it is to anticipate when you might have leaking cans, it’s even trickier to identify and isolate what’s causing them. Every time a can moves, it encounters new risks, and the internal and external liner that protects your aluminum can from the elements starts to break down.
“You have to work through every stage of the manufacturing process to determine where the risks are,” says Jeremy Koehler, Operations Business Specialist at BevSource. “It could be defective materials, a problem with the seaming process, or even a mechanical issue on the line.”
The BevSource team helped narrow down the potential source of one company’s leaking cans after discovering that none of the problem products were found in the 4-packs or 6-packs the company sold. The information that leakers were coming only from the variety packs helped the company narrow the search for issues in the repacking process.
When brands lose the chain of custody or access to direct quality control, additional risk factors come into play. Going through a can broker or purchasing pre-sleeved cans, for example, can make it more challenging to nail down a root cause.
A definitive answer to what’s causing a leaker is never guaranteed. “Even after going through an extensive process of elimination, we still might never know why the cans are leaking,” says Koehler.
3. Don’t Get Them Wet! Even a Little Moisture Can Mean Big Trouble with Leakers
One of the known culprits for causing leaking cans is moisture. Water and other liquids used in the filling and packaging process cause moisture to build up on cans. Without proper drying at various phases, that moisture can cause damage that leads to leakers.
“Frequently, leakers are moisture-related,” says Erika Morehead, Project Manager in Product Development at BevSource. “Unrinsed product or rinse water can get trapped within the secondary packaging and start to attack the packaging or can.”
Depending on which part of the can is exposed to moisture, the integrity of the can could be compromised within hours. “The tab score is the weakest point of the can,” says Jim Kuhr, industry veteran and former Director of Co-Packer Development at BevSource. “Just a little bit of moisture there, and you could develop corrosion that results in the tabs popping.”
4. Leakers Spread Quickly, Destroying Everything They Touch
Stopping moisture damage from spreading is extremely difficult and often requires disposing of products that have been exposed before they contaminate others. Cans are highly susceptible to damage because moisture breaks down the liner, the only thing protecting the aluminum from the corrosive liquid inside.
Marvin-Barnes remembers spending an entire day sorting and repacking products that were exposed to moisture resulting from a leaker. “Once the cans get wet, corrosion starts right away,” says Marvin-Barnes. “You have to sort and segregate any products that have been in contact with a leaker because the damage spreads.”
In this case, many products had to be thrown out. “Once corrosion has started, it’s not going to stop, and those products will also leak inevitably,” says Marvin-Barnes.
5. What’s That Smell? Getting Rid of Leakers Stinks!
Getting rid of those leaking products can be a frightful experience itself, not only because you’re dumping money and product down the drain, but the smell can be rancid. Morehead recalls the shock of uncovering a pallet of beverages damaged by leakers. “It’s horrible,” she says. “ The scents of mold and rotting cardboard along with the sticky residue and flies make for an extremely unpleasant ordeal.”
The experience is so undesirable; it can be hard to find someone who will dispose of leakers. Repackers and freight companies don’t want to handle bad products. You need to investigate and document the damage, but you can’t leave spoiled beverages in a food-grade storage facility, and you don’t want to leave them on a distributor’s or retailer’s dock.
“Uncontrolled damages from a leaker can be incredibly detrimental to a brand,” Morehead goes on, “It’s a hassle that nobody is excited to deal with.”
In addition to the difficulty and expense of transporting bad products, laws govern how alcoholic products can be recycled and destroyed, and there are costs associated with those processes.
6. Leaker Problems Can Paralyze Your Production
Brands with leakers have to allocate resources not only to dispose of products but to find what caused the issue in the first place. Looking into leakers can take your entire team days or weeks, and you will usually want to halt production until you know you’ve removed or minimized the risk of the issue happening again.
Kuhr recalls the strain of investigating leakers as part of an experienced operations team when he was working as the director of operations at a major co-packer. “We had excellent controls and quality checks and maintenance,” says Kuhr. “In the cases when we had mechanical issues, it could take all hands on deck to inspect the often thousands of feet of the conveyor on a production line.”
7. Leaking Liquids Quickly Drain Beverage Budgets
Along with creating a distraction and consuming team resources, leakers cost beverage brands a lot of money. Costs associated with leakers include the price of a potential recall, the cost of disposing of products, fees for legal disputes, and a potential drop in value for existing or future products.
8. A Little Leaker is Enough to Take Down Your Brand in a Big Way
But the immediate financial impact on a beverage doesn’t always reflect the long-term damage leakers can cause to a brand’s relationships with distributors, retailers, customers, and the market. Brands can and do recover from leakers, but it takes work to rebuild trust and brand image, and some beverage brands don’t have the resources to do so.

Best Practices For Eluding Leakers
While many factors play into can quality, there are a few straightforward steps you can take to minimize the risk of long-term business and brand damage from leakers.
Start With Quality
It's critical to vet your can supplier to understand their standards and history of upholding those standards for different product types. Vetting for quality is especially important when considering a supplier that is newer to the market or from a country where quality standards may differ from your specifications. It is also important when you're working with an innovative product or process that requires closer monitoring or tighter measurements.
When you consider the engineering feat that is the aluminum can, the processes required to manufacture and fill cans, and the large production volume of most can lines, it's a miracle leaking cans don't make their way onto store shelves more often. Can manufacturers pay meticulous attention to quality. A case in point is Ball, one of the world's largest beverage can manufacturers, that also designed and built the largest camera NASA has ever flown into space. But even the tightest can manufacturing operations have a margin of error. One in 50,000 cans is defective right off the line, and that is before they are filled and seamed.
The stresses placed on cans change as they move through the production process and into storage, transport, and retail environments. Ultimately, it's the brand owner's responsibility to minimize the probability of leakers by defining and upholding quality standards at every stage of production. Controlling quality has become even more critical as we face an aluminum can shortage.
Your can quality can be significantly impacted by how you proactively protect your cans and how efficiently you investigate and respond to issues like leakers. Adam Smith, Regional Sales Manager at BevSource, encourages brand owners not to overlook what they can learn from looking into leakers.
Investigate Efficiently
As Hannah Krieg, Lab Manager at The Lab, BevSource's pilot facility and full-service laboratory for innovative beverages, says, "An undiscovered leak can cause an undesired chain reaction. If one can at the top of a finished pallet is leaking because of an exterior liner issue, the damage will continue until you identify the source and uncover the cause.” That’s why she says it's essential to have a proactive process to quickly identify, investigate, and address any potential can issues.
How To Address A Leaker
- Review your warranty
Before producing your finished drink, can manufacturers and most contract packers require that you have a can warranty. Warranties are based on corrosion testing performed by the can manufacturer. A warranty means the seller promises the buyer that its cans and ends are free from defects and conform to a seller's specifications. If there is an issue, it can be resolved based on the detailed conditions and limitations outlined in the warranty. Know what's covered by your contract and what requirements you need to uphold to maintain your warranty. Many brand owners are surprised to learn that printing on a can or changing your liner material or formulation means the original can warranty is often no longer valid. Warranties also usually expire within a specified timeframe. - Minimize immediate damage
Take apart pallets from the top down. Primary leakers will likely be found on the top of a pallet. Take apart any pallet with a leaker to identify the primary sources and gather and dispose of any wet products. Once a can has been exposed to the liquid, corrosion begins, so any damp product must go. - Retrace your can journey
Follow your cans back to the start and investigate the manufacturing and filling lines to find any sharp objects that could be damaging your cans. Review the details of your manufacturing processes, from rinsing and packing procedures to the water chemistry on your pasteurizers. Identify anything that could compromise the end quality of your cans. - Take a second look at your specifications
It's always a good idea to review metrics and requirements, like your dissolved oxygen (DO) specifications, with your co-packer. Krieg notes that most of the leakers she sees are related to improper dissolved oxygen levels in the cans. High oxygen levels contribute to elevated can corrosion and perforation risk.
Other can measures and specifications include:
- Corrosion Testing
- SpecMetrix Liner Testing
- Quality Assurance and Quality Control Checkpoints
- Seam Inspections
- Printing Processes
- Formulation Changes
- Liner Material Changes
Once you've completed your investigation and assessed your findings, you will have a solid case with accompanying data to use to address the issue and make the changes necessary to help ensure it doesn't happen again.
Learning from Leakers
Yes, this is all scary stuff, but you don’t have to run away screaming. Like other risk factors that come with being in business, you can learn to effectively reduce the probability of leakers and prepare to mitigate the damage if you have a leaking can. This work will allow you to carry on with a healthy respect for and a realistic perspective on the scary prospect of leakers.
No two leakers are the same. Every leaker you encounter is an opportunity to leverage the scientific process to learn more about the complex art and science required to make and package a beverage. With learning comes improvement.
For Krieg, the challenge is part of the reward. "Food and beverages are complex chemical matrixes," says Krieg. "There is no standard product in food science. Every product is unique and has different quality hurdles. That's what makes it exciting."
As with every aspect of beverage manufacturing, managing your can quality to avoid and mitigate damage from leakers is both an obligation and an opportunity.
"The brands who prioritize and strategize around quality are the ones most prepared to lead with innovation," says Smith. "You can't push against constraints you don't understand how to control."

Do you want to see how you can leverage quality as a competitive advantage for your beverage brand?